O seguinte é un proceso de fabricación completo desde SMT (tecnoloxía de montaxe en superficie) ata DIP (paquete dual en liña), ata detección de IA e ASSY (montaxe), con persoal técnico que proporciona orientación durante todo o proceso. Este proceso abrangue os vínculos fundamentais na fabricación electrónica para garantir unha produción eficiente e de alta calidade.
Proceso de fabricación completo desde SMT→DIP→AI inspection→ASSY
1. SMT (tecnoloxía de montaxe en superficie)
SMT é o proceso principal da fabricación electrónica, usado principalmente para instalar compoñentes de montaxe en superficie (SMD) en PCB.
(1) Impresión de pasta de soldar
Equipamento: impresora de pasta de soldar.
Pasos:
Fixe o PCB no banco de traballo da impresora.
Imprima a pasta de soldadura con precisión nas almofadas do PCB a través da malla de aceiro.
Comprobe a calidade da impresión da pasta de soldadura para asegurarse de que non hai offset, falta de impresión ou sobreimpresión.
Puntos clave:
A viscosidade e o grosor da pasta de soldadura deben cumprir os requisitos.
A malla de aceiro debe ser limpada regularmente para evitar obstrucións.
(2) Colocación de compoñentes
Equipo: Pick and Place Machine.
Pasos:
Cargue os compoñentes SMD no alimentador da máquina SMD.
A máquina SMD recolle os compoñentes a través da boquilla e colócaos con precisión na posición especificada do PCB segundo o programa.
Comprobe a precisión da colocación para asegurarse de que non hai desplazamentos, pezas incorrectas ou pezas que faltan.
Puntos clave:
A polaridade e dirección dos compoñentes deben ser correctas.
A boquilla da máquina SMD debe manterse regularmente para evitar danos nos compoñentes.
(3) Soldadura por refluxo
Equipamento: Forno de soldadura por refluxo.
Pasos:
Envía o PCB montado ao forno de soldadura por refluxo.
Despois de catro etapas de prequecemento, temperatura constante, refluxo e arrefriamento, a pasta de soldadura fúndese e fórmase unha xunta de soldadura fiable.
Comprobe a calidade da soldadura para asegurarse de que non hai defectos como xuntas de soldadura en frío, pontes ou lápidas.
Puntos clave:
A curva de temperatura da soldadura por refluxo debe optimizarse segundo as características da pasta de soldadura e os compoñentes.
Calibrar a temperatura do forno regularmente para garantir unha calidade de soldadura estable.
(4) Inspección AOI (inspección óptica automática)
Equipamento: instrumento automático de inspección óptica (AOI).
Pasos:
Escanee ópticamente a PCB soldada para detectar a calidade das unións de soldadura e a precisión de montaxe dos compoñentes.
Rexistrar e analizar defectos e retroalimentación ao proceso anterior para o axuste.
Puntos clave:
O programa AOI debe ser optimizado segundo o deseño do PCB.
Calibra o equipo regularmente para garantir a precisión da detección.
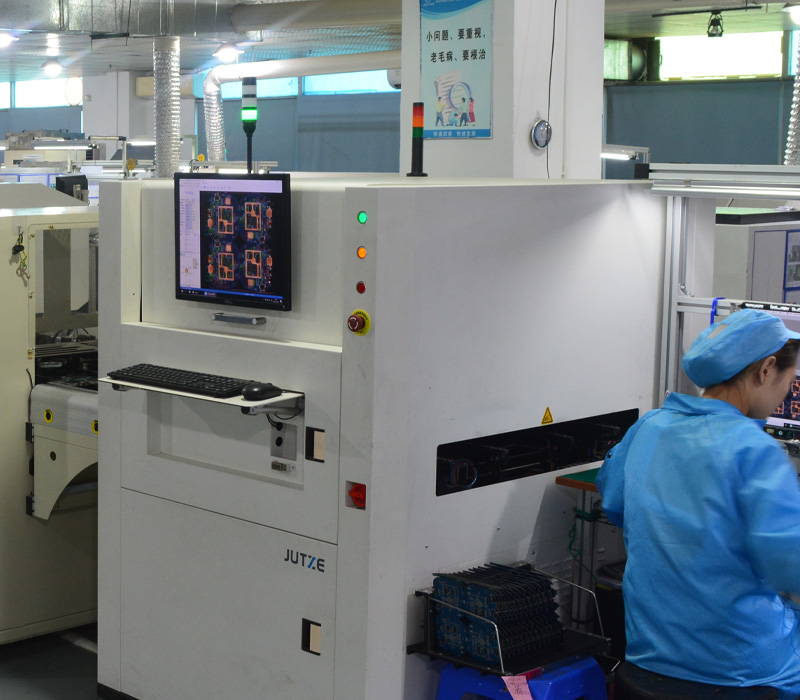
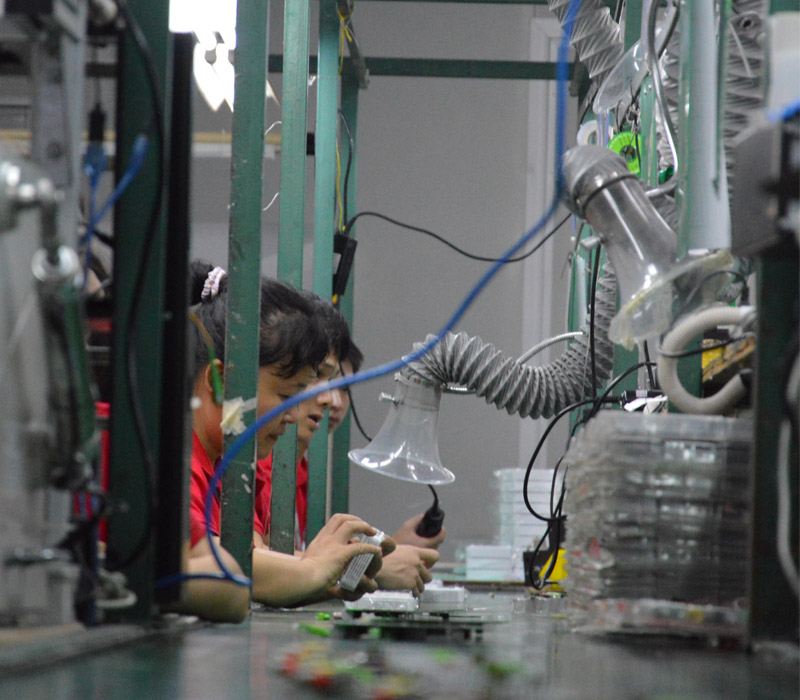
2. Proceso DIP (paquete dual en liña).
O proceso DIP úsase principalmente para instalar compoñentes de orificio pasante (THT) e adoita utilizarse en combinación co proceso SMT.
(1) Inserción
Equipamento: máquina de inserción manual ou automática.
Pasos:
Insira o compoñente do orificio pasante na posición especificada da PCB.
Comprobe a precisión e estabilidade da inserción dos compoñentes.
Puntos clave:
Os pinos do compoñente deben cortarse á lonxitude adecuada.
Asegúrese de que a polaridade dos compoñentes sexa correcta.
(2) Soldadura por onda
Equipamento: forno de soldadura por onda.
Pasos:
Coloque o PCB enchufable no forno de soldadura por ondas.
Soldar os pinos dos compoñentes ás almofadas da PCB mediante soldadura por onda.
Comprobe a calidade da soldadura para asegurarse de que non hai xuntas de soldadura en frío, pontes ou fugas.
Puntos clave:
A temperatura e a velocidade da soldadura por ondas deben optimizarse segundo as características do PCB e dos compoñentes.
Limpe o baño de soldadura regularmente para evitar que as impurezas afecten a calidade da soldadura.
(3) Soldadura manual
Repare manualmente o PCB despois da soldadura por ondas para reparar defectos (como xuntas de soldadura en frío e pontes).
Use un soldador ou pistola de aire quente para soldar local.
3. Detección de intelixencia artificial (detección de intelixencia artificial)
A detección AI úsase para mellorar a eficiencia e precisión da detección de calidade.
(1) Detección visual AI
Equipamento: sistema de detección visual AI.
Pasos:
Captura imaxes de alta definición do PCB.
Analiza a imaxe mediante algoritmos de IA para identificar defectos de soldadura, compensación de compoñentes e outros problemas.
Xera un informe de proba e remíteo ao proceso de produción.
Puntos clave:
O modelo de IA debe ser adestrado e optimizado en función dos datos de produción reais.
Actualiza o algoritmo de IA regularmente para mellorar a precisión da detección.
(2) Probas funcionais
Equipamento: Equipo de proba automatizado (ATE).
Pasos:
Realice probas de rendemento eléctrico no PCB para garantir as funcións normais.
Rexistrar os resultados das probas e analizar as causas dos produtos defectuosos.
Puntos clave:
O procedemento de proba debe deseñarse segundo as características do produto.
Calibre regularmente o equipo de proba para garantir a precisión da proba.
4. Proceso ASSY
ASSY é o proceso de ensamblaxe de PCB e outros compoñentes nun produto completo.
(1) Montaxe mecánica
Pasos:
Instale a PCB na carcasa ou soporte.
Conecte outros compoñentes como cables, botóns e pantallas de visualización.
Puntos clave:
Asegurar a precisión da montaxe para evitar danos no PCB ou outros compoñentes.
Use ferramentas antiestáticas para evitar danos estáticos.
(2) Queima de software
Pasos:
Grava o firmware ou o software na memoria da PCB.
Comprobe os resultados da gravación para asegurarse de que o software funciona normalmente.
Puntos clave:
O programa de gravación debe coincidir coa versión do hardware.
Asegúrese de que o ambiente en queima é estable para evitar interrupcións.
(3) Probas de máquina enteira
Pasos:
Realizar probas funcionais nos produtos ensamblados.
Comprobe o aspecto, o rendemento e a fiabilidade.
Puntos clave:
Os elementos da proba deben cubrir todas as funcións.
Rexistra os datos das probas e xera informes de calidade.
(4) Embalaxe e envío
Pasos:
Embalaxe antiestática de produtos cualificados.
Etiquetar, empacar e preparar para o envío.
Puntos clave:
Os envases deben cumprir os requisitos de transporte e almacenamento.
Rexistra a información de envío para facilitar a rastrexabilidade.

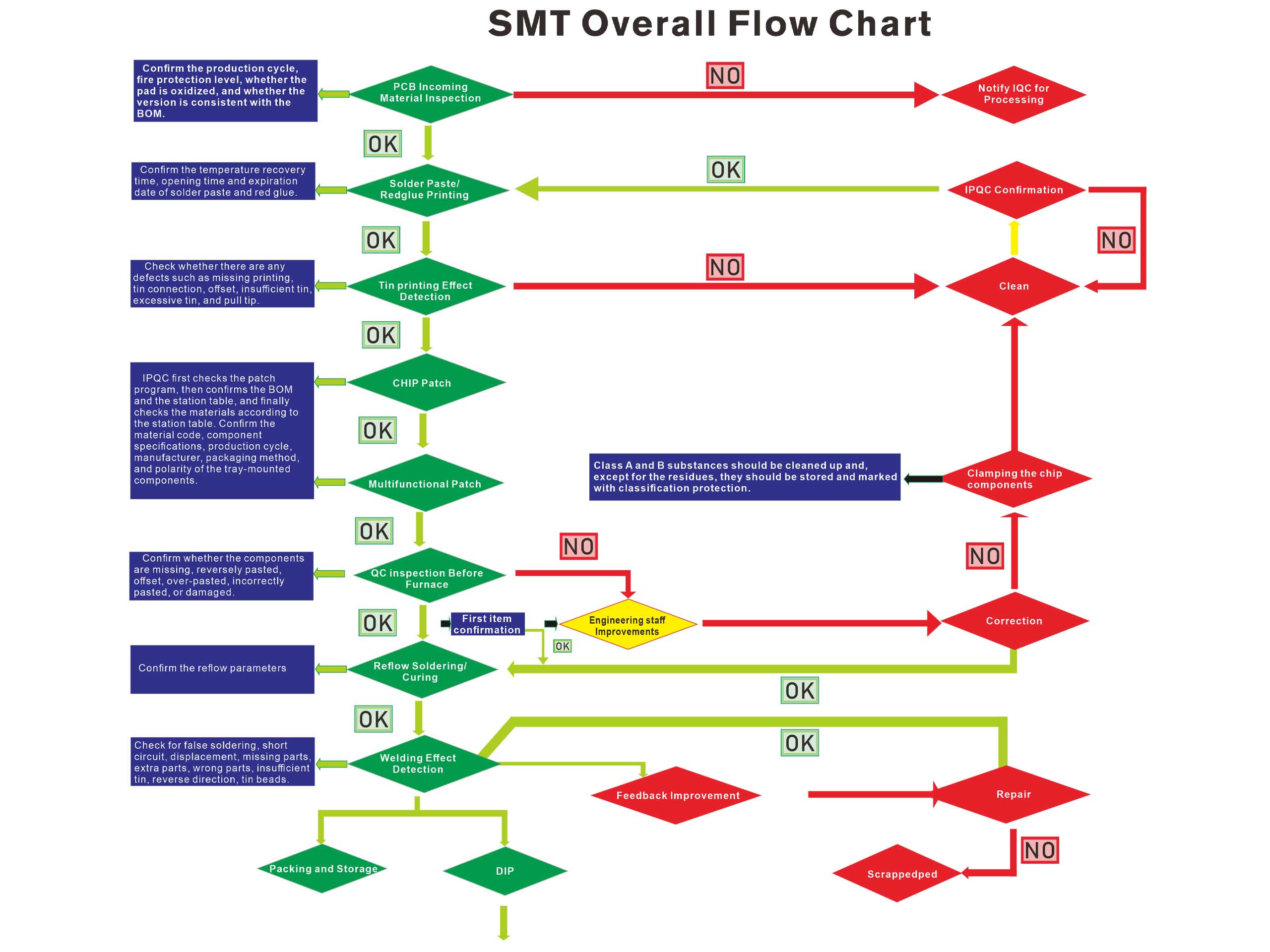
5. Puntos clave
Control ambiental:
Evita a electricidade estática e utiliza equipos e ferramentas antiestáticas.
Mantemento de equipos:
Manteña e calibra regularmente equipos como impresoras, máquinas de colocación, fornos de refluxo, fornos de soldadura por onda, etc.
Optimización de procesos:
Optimizar os parámetros do proceso segundo as condicións reais de produción.
Control de calidade:
Cada proceso debe ser sometido a unha estrita inspección de calidade para garantir o rendemento.